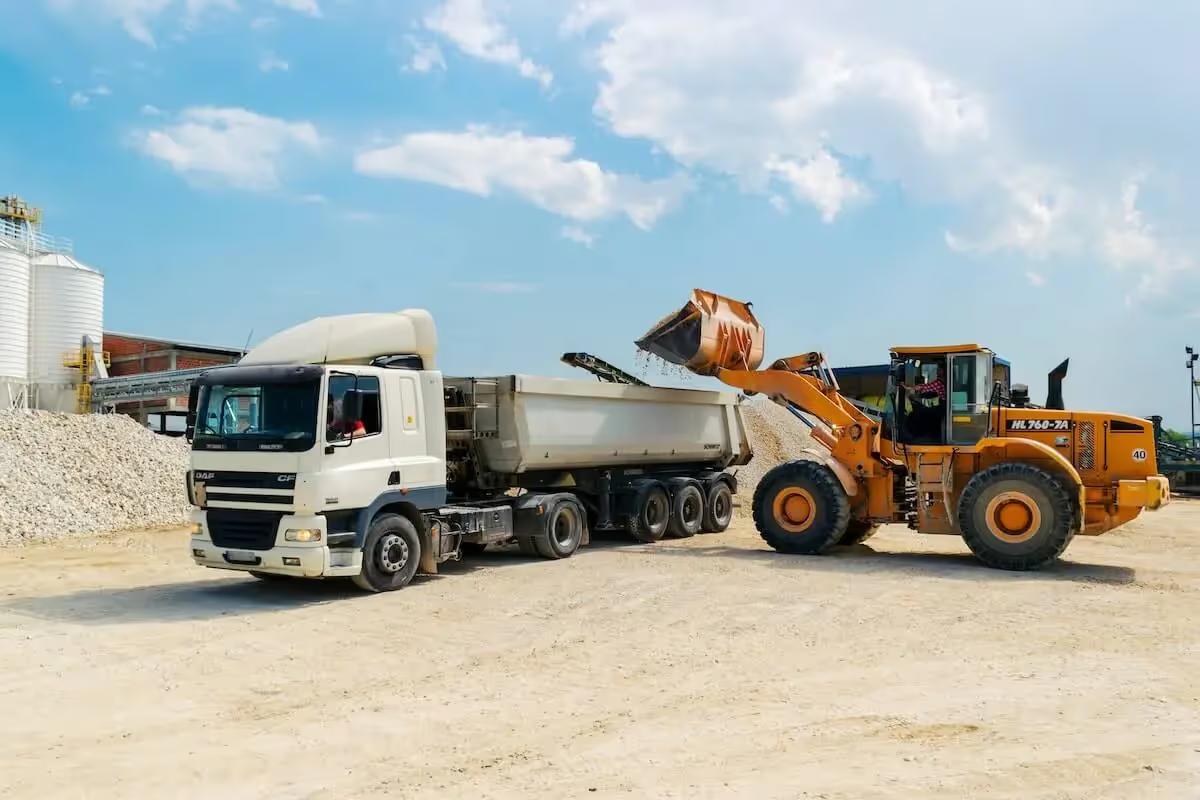
En tant que chef de carrière, la continuité de votre ligne de production est un enjeu majeur. La maintenance en est un puissant levier : plus vous intervenez vite et efficacement, plus l'incident pourra être clôturé rapidement.
Nous partageons dans cet article les 5 KPI de maintenance industrielle à connaître absolument pour analyser le degré de performance d'un service de maintenance, d'une équipe technique ou d'un technicien, au regard de la capacité de réaction dans le traitement et la gestion des anomalies pouvant survenir dans les moyens techniques.
1. Évaluer la fiabilité des équipements
On utilise ici l'indicateur MTBF ou Mean Time Between Failure. En d'autres termes, il s'agit de mesurer l'intervalle de temps entre les défaillances de vos machines.
Le calcul est le suivant : temps de fonctionnement total / nombre de pannes
Par exemple, si sur 3 mois, votre machine a fonctionné durant 225 heures et a cumulé 10 pannes, ce qui représente 20 heures de pannes.
On prend le temps sur lequel la machine a effectivement fonctionné : 225 - 20 = 205
On divise ce temps par le nombre de pannes : 205 / 10 = 20,5
Cet indicateur vous permettra :
- d'anticiper les pannes de vos machines
- de déterminer si votre machine est obsolète et si vous devez investir dans une nouvelle.
Vous pouvez également le compléter avec le taux de défaillance.
Le calcul est le suivant : nombre de pannes / temps de fonctionnement total x 100
Si on reprend notre exemple : 10 / 225 x 100 = 4,4%
2. Mesurer l'efficacité des interventions
On utilise l'indicateur MTTR ou Mean Time to Repair, soit le temps de réparation pour les plus francophones. En d'autres termes, vous mesurez le temps passé en moyenne sur une intervention de maintenance.
Le calcul est le suivant : somme du temps des opérations de maintenance / nombre d'opérations de maintenance
Par exemple, si votre équipe a mené 5 interventions qui ont duré 2 heures chacune :
On calcule le temps de maintenance total : 2 x 5 = 10
Puis on calcule le taux de réparation : 10 / 5 = 2
Cet indicateur vous permettra de :
- mesurer l'efficacité de vos opérations de maintenance
- contrôler la maintenabilité des équipements
3. Estimer la capacité à réagir face à un incident
Ici, on peut utiliser différents indicateurs tous basés sur le temps écoulé.
Entre l'incident et sa détection
Il est possible d’être rapidement au courant grâce à l’insertion de réseaux de capteurs qui génèrent des alertes par e-mail, par SMS ou sur votre logiciel de gestion.
Entre la détection et le lancement de l'ordre de travail
Pour réduire ce temps au maximum, vous pouvez créer des modèles d'ordre ou utiliser des outils digitaux pour communiquer plus rapidement.
Entre l'ordre de travail et le début de l'intervention
Les process doivent avoir été clarifiés en amont pour faciliter une réactivité sans faille.
Entre le début de l'intervention et le diagnostic
Les compétences du technicien jouent beaucoup ici, mais ne sont pas les seuls facteurs. La qualité de la documentation technique, la facilité d'accès à la machine, le support client de votre fournisseur, sont aussi des éléments à prendre en compte.
Si la carrière est bien équipée, le technicien peut retrouver sur son téléphone l'historique des incidents, les rapports, la stratégie de recherche, à partir d'une base de données techniques commune.
4. Déterminer le rendement de votre équipement
On utilise ici le taux de rendement synthétique. En d'autres mots, il permet d'évaluer la différence entre la production théorique d'un équipement et sa production réelle.
Le calcul est le suivant : fonctionnement x performance x qualité
Voici comment calculer les variables intermédiaires :
- le taux de fonctionnement : temps brut / temps théorique x 100
- le taux de performance : temps net / temps brut x 100
- le taux de qualité : temps utile / temps net x 100
Temps théorique ou total : la machine fonctionne 100% du temps
- moins les heures de fermeture de la carrière = temps d'ouverture
- moins les arrêts planifiés (maintenance programmée...) = temps requis
- moins les pannes = temps brut
- moins les micro-arrêts (pauses, nettoyage...) = temps net
- moins le temps passé à produire des rebuts ou à retoucher une production non qualitative = temps utile
Par exemple, si le temps théorique est de 100h, le temps brut de 80h, le temps net de 70h et le temps utile de 50h :
- le taux de fonctionnement : 80 / 100 x 100 = 80%
- le taux de performance : 70 / 80 x 100 = 87,5%
- le taux de qualité : 50 / 70 x 100 = 71,4%
Cet indicateur est particulièrement dépendant du calendrier, notamment des jours fériés et des congés, des évolutions de la demande et donc de la production, des ruptures de stocks, etc.
5. Calculer les coûts de maintenance
Cet indicateur est en fait une somme de coûts :
- les coûts directs, comme les pièces détachées mais aussi la main-d’œuvre interne ou en sous-traitance
- les coûts indirects, comme l'arrêt de la production
Cette somme vous permet ensuite d'estimer le ROI de l'acquisition d'une nouvelle machine en comparaison du coût de votre machine actuelle.
En conclusion, les indicateurs de maintenance industrielle servent à analyser les résultats et à prendre des décisions optimisées. Ils sont indispensables pour améliorer les temps de chargement, de communication, de déplacement ou d'attente sur un chantier.
👉 Découvrez les solutions de Busit et optimisez vos KPI de maintenance pour un rendement maximal !
Pour mettre en place des KPI de suivi facilement et rapidement, nous vous recommandons d'utiliser une solution digitale. Nos équipes sont disponibles pour discuter avec vous de vos besoins et de votre plan d'actions. Pour être recontacté gratuitement, c'est par ici !
Vous ne voulez rien rater de l'actualité de notre secteur ? Synaxe lance Bascule : la newsletter qui fait basculer vos godets !