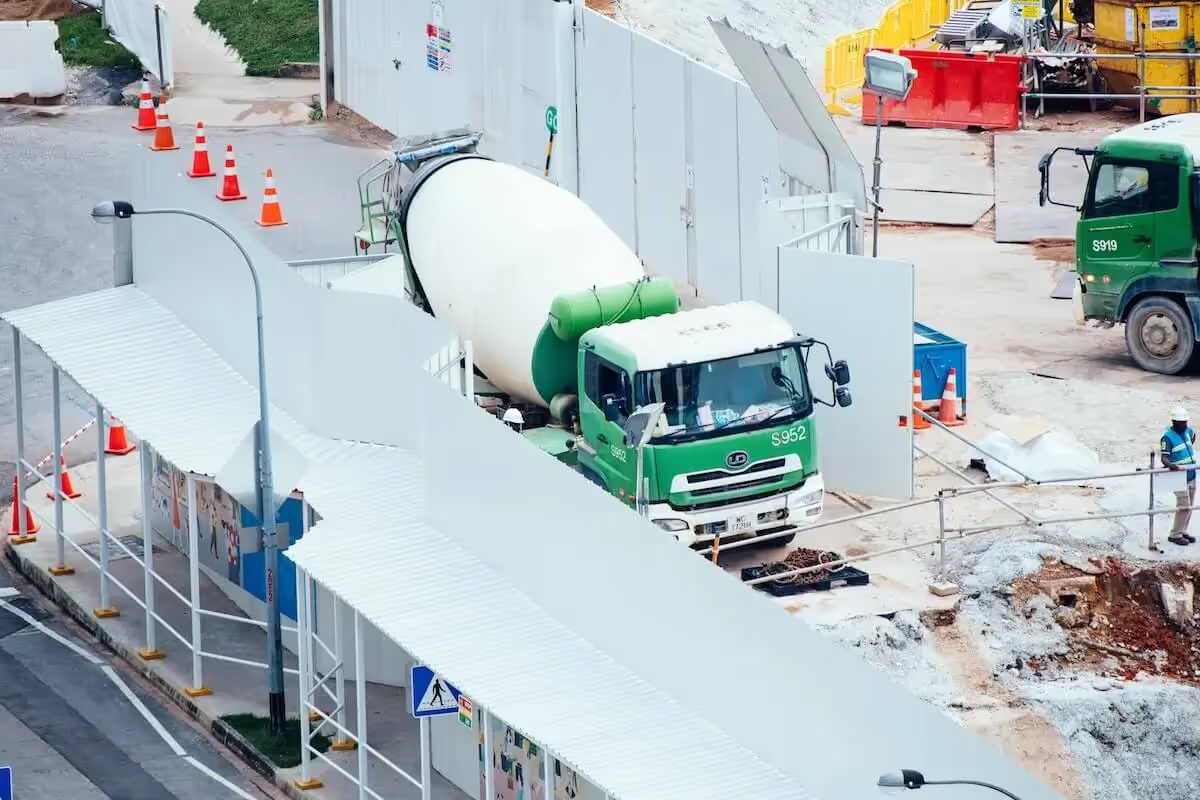
The concrete delivery note and its digital alternatives
The concrete delivery note is just a simple sheet of paper, and yet it is essential for the smooth delivery. The problem is that construction site conditions are not always optimal for rigorous monitoring... And the slightest mistake can slow down the entire process.
What if we told you that there was a solution to make concrete delivery smoother and more reliable? Specialist in the digitalization of the building materials industry, Synaxe Tell you all its secrets in this article.
Focus on the concrete delivery note, the cornerstone of customer relationships
What is the role of the concrete delivery note? Why is it so important? Let's take stock of this essential element for monitoring the construction site.
Complex implementation
The concrete is a very common building material. Natural and inert, it does not present any danger when hardened. On the other hand, any handling of fresh concrete involves risks for the eyes and skin: burns, redness, allergies, etc. This is why workers must take precautions to work safely:
- Wear appropriate clothing: waterproof clothing, protective goggles, waterproof gloves, knee pads, boots and a helmet.
- Respect good hygiene: regular washing of work clothes, frequent hand washing and showering at the end of the day.
In addition, the use of concrete is subject to specific constraints and standards. The material delivered must fully comply with the customer's request, and therefore meet a strict quality control.
A necessary follow-up
This complexity of concrete structures gives rise to a high level of requirement. To ensure the correct use of the material and the smooth execution of the order, site managers must coordinate the teams while ensuring compliance with the constraints. And that's where the concrete delivery note intervenes: in fact, it makes it possible to follow all the information necessary for the proper monitoring of the concreting.
Establishing a tracking sheet is a long and tedious task. The information must be accurate, reliable and comprehensive despite the difficult conditions of the construction site. Delayed delivery, pen lost in your pocket, forgotten confirmation email: the slightest mistake can slow down the entire process.
How can you get around this difficulty and save time during delivery?
Let's take a closer look at it...
An update on the regulations governing the concrete delivery note
What standards do you need to know? How to ensure the smooth running of the delivery? What information should appear on the tracking sheet? Reminder of the regulations in force.
Overview of concrete standards
A good relationship between the supplier and the construction company ensures a lasting structure. La European standard is an essential tool to achieve this goal.
According to the standard NF IN 206-1, it is the company that is responsible for placing the concrete in the structure.
The execution of the work must follow the rules of the art, governed by several standards such as NF DTU 21 Or the NF DTU 13.3.
For its part, concrete sampling is carried out in accordance with the standard NF EN 12350-1. In order to avoid the appearance of defects such as cracking, the concrete is subjected to a battery of tests (visual inspection, measurement of the consistency of fresh concrete, measurement of compression of hardened concrete, etc.).
But there are shortcomings in the European standard. This is why the representatives of concrete users (UMGO, EGF-BTP, FNTP and SNBPE) signed the charter of good relationships between suppliers and users of ready-to-use concrete (BPE). Regularly updated, it establishes a precise protocol, which defines, among other things:
- Information that the producer owes to the user.
- Definitions of concrete batches.
- The duration of use and the impact of delivery times.
- Access to construction site safety.
The essential steps for the smooth running of a concrete delivery
What are the boxes to check for a successful concrete delivery?
Before reception:
- The supplier and the company agree on the date, time and delivery rate of the concrete.
- The supplier informs the company about the methods of installation, the presence of special transports and the limitations on the type of delivery vehicle.
- If necessary, it also transmits information on the composition of concrete: type of cement, aggregates and additives, strength class, water/cement ratio, origin of the components, etc.
- The health risks of handling fresh concrete must be indicated by the producer.
At the reception:
- Concrete is subject to various controls in order to verify compliance with market requirements.
- There are two types of controls: those whose results are known before the concrete is put in place (visual inspection, measurement of air content, measurement of consistency), and those whose results are known after the concrete has been put in place (measurement of resistance to compression).
- The frequency of checks is determined by the NF DTU 21.
- If the material does not comply with the concrete delivery note, the company can return the router and apply the conditions set out in the contract.
Information that should appear on the concrete delivery note
Here is the essential information for monitoring concrete construction:
- The name of the concrete plant.
- The name of the concrete manufacturing plant.
- The serial number on the delivery note.
- The identification of the delivery vehicle.
- The name of the purchaser.
- The reference and coordinates of the site.
- The quantity of concrete (in cubic meters).
- Concrete references.
- The declaration of conformity of concrete and the reference to the specifications and the standard NF IN 206-1.
- If necessary, the logo or the name of the certification body.
- The time the concrete arrives at the construction site.
- The date and time of loading (to know the first contact between cement and water).
- The start and end time of unloading.
Note: the delivery note must be signed only after receipt and implementation.
The advantages of good dematerialized concrete
The dematerialized voucher is not printed on paper: it is displayed directly on the smartphone of the driver in charge of the order. But what are the benefits of going digital?
A considerable time saver
Thanks to the dematerialized delivery note, the driver can manage everything from his smartphone or tablet. The simplified entry system allows him to write down information quickly while reducing his margin of error. Once the concrete is delivered, there is nothing to report: the data is automatically synchronized on the computer!
More reliable data
If the information is processed more quickly, it is also more accurate. Throughout the process, both the driver and the customer have access to delivery status and concrete monitoring indicators. Delays are notified in real time and calculations are automated, which limits the risk of human error.
But the advantages of the dematerialized delivery note do not end once the delivery has been made. As the information is automatically sorted, document preparation is facilitated. Statistics on delivery times also make it possible to consolidate a continuous improvement process, and therefore to develop your business!
An optimized customer experience
The dematerialized delivery note brings a breath of modernity to your business. Vector of fluidity and flexibility, it positions you as a serious and innovative partner. By showing your customers that you are on the lookout for new features and that you are updating your services, you stand out from the competition.
Connected delivery: take the plunge with Synaxe
Discover the digital solution SX Delivery, a dematerialized concrete delivery note that opens up new perspectives.
SX Delivery, between innovation and ease of use
SX Delivery is a solution developed by Synaxe, specialist in the digitalization of the building materials industry.
It is based on two key tools:
- The application Delivery App, which allows the driver to receive concrete delivery notes and have them signed on their mobile phone.
- The interface SX Delivery Cloud, which allows delivery notes to be consulted in real time. It is connected to your company's business tools (schedules, management tools, third-party systems).
How does that work in practice?
The Synaxe concrete delivery note adapts to the specificities of your business. It sets the pace for each stage of delivery:
- Confirmation of loading : when production starts, the concrete delivery note is generated. The driver receives it on his smartphone as soon as he picks up the order.
- Arrival at the place of delivery and start of loading : as soon as the power plant leaves, the delivery vehicle is geolocated.
- End of upload and signature : the customer signs the concrete delivery note on the driver's mobile phone. Delivery information is automatically added to the application, but the driver can add details if needed. The data is transmitted in real time on the client's dashboard. They remain accessible on a web portal in the form of automatically generated documents (delivery note in PDF format with legal signature). The customer is billed immediately.
- Departure from the construction site and return to the power plant : geolocation makes it possible to anticipate the return of the delivery truck.
The advantages of the Synaxe concrete delivery note
In recent years, numerous digital solutions have appeared on the market... but SX Delivery is the only one specially designed for the building materials industry: quarries, concrete plants, recycling platforms and sites for recovering soil from the excavation of construction sites.
And for good reason, Synaxe has been evolving in the sector for 20 years, with 215 power plants. Today, our tool is used by 2,000 drivers and it is the source of more than 10,000 delivery notes per day!
This experience in the field, enriched by feedback from our customers, has allowed us to develop a solution that is perfectly adapted to this very particular industry. SX Delivery is activated immediately, but its wide range of parameters allows it to be precisely adjusted to the specificities of your operating site.
To help you take the digital leap, a dedicated contact person helps you get started with the tool and create a tailor-made solution. In the event of a glitch, you can trust our dedicated maintenance team.
Want to know more? Without further ado, contact us to discuss transparently which solutions are best suited to your business.