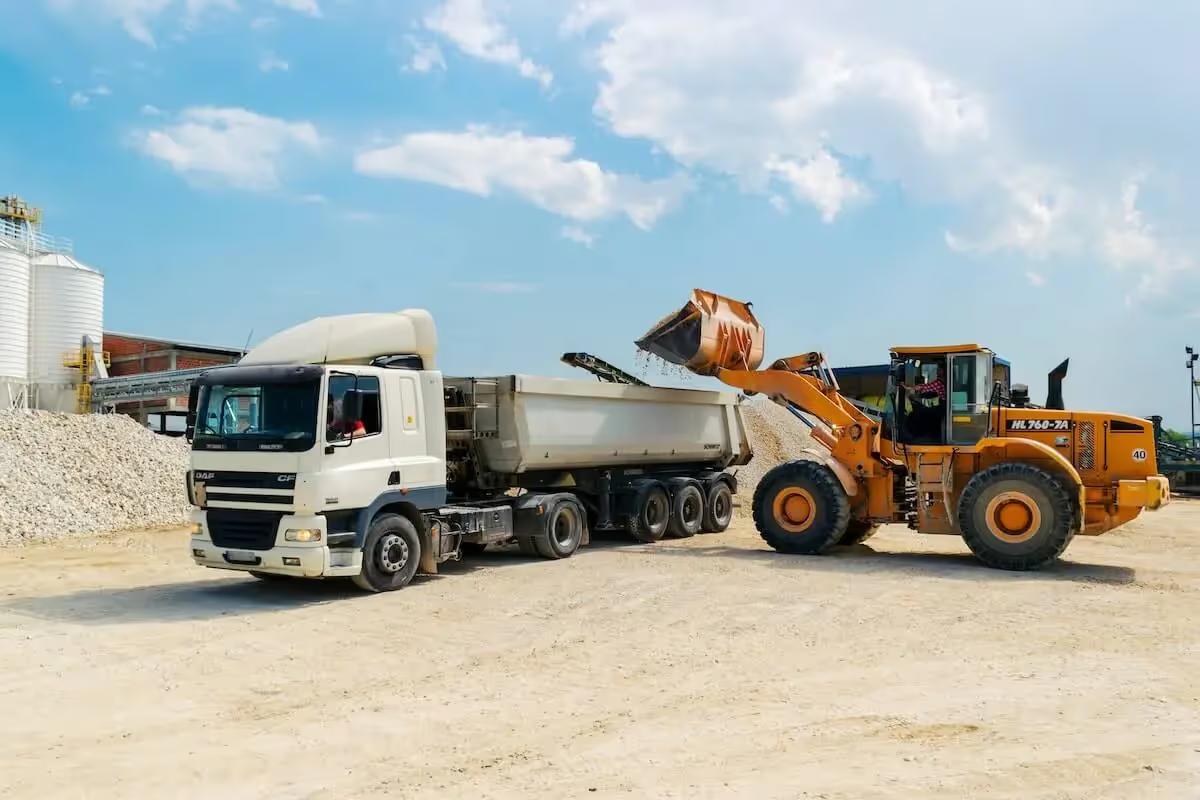
As a career manager, the continuity of your production line is a major challenge. La maintenance is a powerful lever: the more quickly and effectively you intervene, the more quickly the incident can be closed.
In this article, we share the 5 industrial maintenance KPIs It is essential to know in order to analyze the degree of performance of a maintenance service, a technical team or a technician, in terms of the capacity to react in the treatment and management of anomalies that may occur in technical resources.
1. Evaluate the reliability of equipment
Here we use the indicator MTBF or Mean Time Between Failure. In other words, it's about measuring the time interval between the failures of your machines.
The calculation is as follows: total operating time/number of failures
For example, if over 3 months, your machine worked for 225 hours and accumulated 10 failures, which represents 20 hours of failures.
We take the time on which the machine actually worked: 225 - 20 = 205
We divide this time by the number of failures: 205/10 = 20.5
This indicator will allow you to:
- to anticipate the breakdowns of your machines
- to determine if your machine is obsolete and if you need to invest in a new one.
You can also complete it with the failure rate.
The calculation is as follows: number of failures/total operating time x 100
If we go back to our example: 10/225 x 100 = 4.4%
2. Measuring the effectiveness of interventions
We use the indicator MTTR or Mean Time to Repair, which is the repair time for the most French-speaking. In other words, you measure the average time spent on a maintenance intervention.
The calculation is as follows: Sum of the time of maintenance operations/number of maintenance operations
For example, if your team carried out 5 interventions that lasted 2 hours each:
We calculate the total maintenance time: 2 x 5 = 10
Then we calculate the repair rate: 10/5 = 2
This indicator will allow you to:
- measure the effectiveness of your maintenance operations
- check the maintainability of equipment
3. Evaluate the ability to respond to an incident
Here, we can use various indicators all based on the time elapsed.
Between the incident and its detection
It is possible to be quickly up to date thanks to the insertion of sensor networks that generate alerts by e-mail, SMS or on your management software.
Between detecting and launching the work order
To reduce this time as much as possible, you can create order models or use digital tools to communicate more quickly.
Between the work order and the start of the intervention
The processes must have been clarified in advance to facilitate seamless reactivity.
Between the start of the procedure and the diagnosis
Technician skills play a lot here, but they're not the only factors. The quality of the technical documentation, the ease of access to the machine, the customer support of your supplier, are also elements to take into account.
If the career is well equipped, the technician can find on his phone the history of incidents, reports, and search strategy, from a common technical database.
4. Determine the performance of your equipment
Here we use the synthetic rate of return. In other words, it makes it possible to assess the difference between the theoretical production of an equipment and its real production.
The calculation is as follows: function x performance x quality
Here's how to calculate the intermediate variables:
- The rate of operation: gross time/theoretical time x 100
- The rate of performance: net time/gross time x 100
- The rate of quality: useful time/net time x 100
Theoretical or total time: the machine works 100% of the time
- minus the closing hours of the quarry = opening time
- minus planned shutdowns (scheduled maintenance...) ) = time required
- minus breakdowns = Gross time
- Minus micro-shutdowns (breaks, cleaning...) ) = Net time
- minus the time spent producing scrap or retouching non-qualitative production = Useful time
For example, if the theoretical time is 100 hours, the gross time is 80 hours, the net time is 70 hours and the useful time is 50 hours:
- the operating rate: 80/100 x 100 = 80%
- the performance rate: 70/80 x 100 = 87.5%
- the quality rate: 50/70 x 100 = 71.4%
This indicator is particularly dependent on the calendar, in particular holidays and holidays, changes in demand and therefore production, stock shortages, etc.
5. Calculate maintenance costs
This indicator is in fact a sum of costs:
- The direct costs, such as spare parts but also internal or subcontracted labour
- The indirect costs, such as the cessation of production
This sum then allows you to estimate the KING of the acquisition of a new machine compared to the cost of your current machine.
In conclusion, the industrial maintenance indicators are used to analyze results and to make optimized decisions. They are essential to improve loading, communication, travel or waiting times on a construction site.
To set up monitoring KPIs easily and quickly, we recommend using a digital solution. Our teams are available to discuss your needs and your action plan with you. To be contacted again for free, click here!
Do you want to miss out on any of the latest news in our sector? Synaxe launches Bascule: the newsletter that makes your buckets tip over!